Plastic extrusion for budget-friendly product fabrication
Plastic extrusion for budget-friendly product fabrication
Blog Article
A Comprehensive Guide to the Process and Advantages of Plastic Extrusion
In the substantial realm of manufacturing, plastic extrusion emerges as a highly effective and vital procedure. Altering raw plastic into constant accounts, it caters to a wide variety of markets with its remarkable adaptability.
Recognizing the Basics of Plastic Extrusion
While it may appear complicated at initial glance, the process of plastic extrusion is basically simple. The process starts with the feeding of plastic product, in the form of powders, granules, or pellets, right into a heated barrel. The shaped plastic is after that cooled, solidified, and cut right into preferred sizes, completing the procedure.
The Technical Refine of Plastic Extrusion Explained

Types of Plastic Suitable for Extrusion
The selection of the appropriate kind of plastic is a crucial aspect of the extrusion process. Different plastics supply unique homes, making them more suited to particular applications. Polyethylene, for instance, is typically made use of as a result of its inexpensive and easy formability. It provides excellent resistance to chemicals and dampness, making it suitable for products like tubes and containers. Polypropylene is an additional preferred selection due to its high melting point and resistance to tiredness. For even more durable applications, polystyrene and PVC (polyvinyl chloride) are usually chosen for their stamina and resilience. These are common alternatives, the option eventually depends on the certain demands of the item being created. Understanding these plastic kinds can considerably enhance the extrusion procedure.
Contrasting Plastic Extrusion to Other Plastic Forming Methods
Understanding the kinds of plastic appropriate for extrusion paves the method for a wider discussion on just how plastic extrusion piles up against various other plastic developing methods. Plastic extrusion is unparalleled when it comes to producing continual profiles, such as gaskets, pipelines, and seals. It Learn More likewise allows for a regular cross-section along the length of the product.
Trick Advantages of Plastic Extrusion in Manufacturing
In the realm of manufacturing, plastic extrusion uses several considerable benefits. One notable benefit is the cost-effectiveness of the process, that makes it an economically appealing production approach. Additionally, this method gives remarkable product versatility and enhanced production rate, therefore increasing overall manufacturing performance.
Cost-Effective Production Method
Plastic extrusion leaps to the center as a cost-effective manufacturing method in production. This procedure sticks out for its ability to generate high volumes of material rapidly and successfully, supplying manufacturers with significant savings. The main cost advantage is the capability to utilize much less expensive raw products. Extrusion uses thermoplastic materials, which are much less pricey contrasted to ceramics or steels. Additionally, the extrusion process itself is fairly simple, reducing labor prices. Additionally, plastic extrusion needs much less energy than traditional manufacturing approaches, adding to reduced functional costs. The process additionally lessens waste, as any defective or excess materials can be reused and reused, supplying an additional layer of cost-effectiveness. Generally, the financial benefits make plastic extrusion an extremely eye-catching choice in the manufacturing industry.
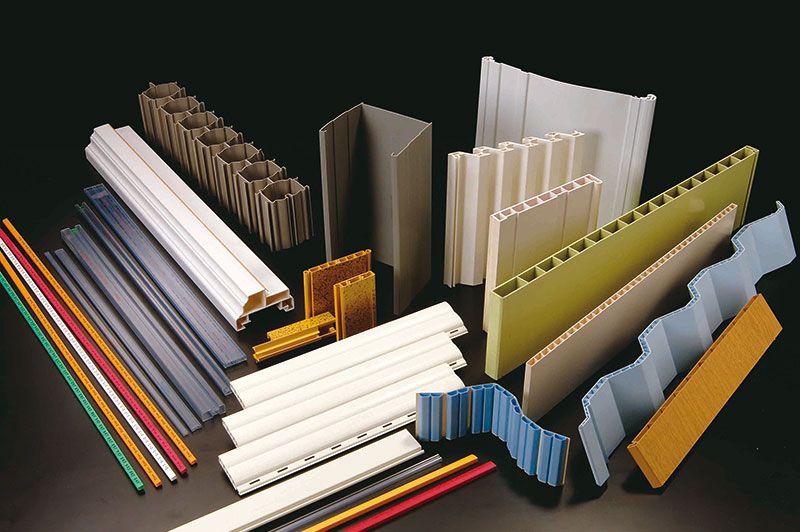
Superior Product Versatility
Past the cost-effectiveness of plastic extrusion, another substantial benefit in manufacturing lies in its premium product flexibility. This makes plastic extrusion a suitable option for markets that require tailored plastic elements, such as auto, building, and packaging. In significance, plastic extrusion's product versatility cultivates advancement while enhancing operational performance.
Improved Production Rate
A considerable benefit of plastic extrusion lies in its boosted production speed. This production procedure enables for high-volume production in a fairly short time period. It is capable of producing long, constant plastic profiles, which substantially reduces the manufacturing time. This high-speed manufacturing is specifically helpful in sectors where large amounts of plastic components are required within limited deadlines. Couple of various my review here other production procedures can match the rate of plastic extrusion. In addition, the ability to preserve constant high-speed production without compromising product high quality establishes plastic extrusion in addition to various other methods. The enhanced production speed, consequently, not only allows suppliers to satisfy high-demand orders yet also adds to Go Here raised effectiveness and cost-effectiveness. This helpful feature of plastic extrusion has made it a recommended option in many markets.
Real-world Applications and Impacts of Plastic Extrusion
In the realm of manufacturing, the strategy of plastic extrusion holds profound significance. The economic benefit of plastic extrusion, primarily its cost-effective and high-volume result, has changed production. The industry is persistently striving for innovations in naturally degradable and recyclable products, suggesting a future where the benefits of plastic extrusion can be maintained without endangering ecological sustainability.
Verdict
In conclusion, plastic extrusion is a reliable and highly effective approach of transforming resources into diverse items. It offers numerous benefits over various other plastic forming techniques, consisting of cost-effectiveness, high outcome, marginal waste, and style versatility. Its impact is greatly felt in different sectors such as building, automotive, and customer items, making it a crucial process in today's manufacturing landscape.
Diving deeper into the technological process of plastic extrusion, it begins with the option of the appropriate plastic product. When cooled down, the plastic is reduced right into the called for sizes or wound onto reels if the product is a plastic movie or sheet - plastic extrusion. Contrasting Plastic Extrusion to Other Plastic Forming Techniques
Comprehending the types of plastic ideal for extrusion paves the means for a wider conversation on just how plastic extrusion stacks up versus other plastic forming approaches. Couple of various other manufacturing processes can match the rate of plastic extrusion.
Report this page